Are your pipelines silently corroding, costing you time, money, and potentially jeopardizing safety? Implementing a robust corrosion prevention strategy is no longer optional; it's an imperative for pipeline integrity and longevity.
The integrity of pipelines is paramount, especially in industries dealing with the transportation of critical resources. Corrosion, both galvanic and microbial, represents a persistent threat, leading to costly repairs, downtime, and potential environmental hazards. A comprehensive approach to corrosion management necessitates a deep understanding of the available protection methods, including the strategic deployment of flange isolation kits (FIKs) and monolithic isolation joints (MIJs). This analysis delves into the critical aspects of FIKs, exploring their design, application, advantages, and limitations, while also providing guidance on optimal selection, installation, and management practices.
Aspect | Details |
---|---|
Topic | Flange Isolation Kits (FIKs) for Pipeline Corrosion Prevention |
Industry Focus | Oil and Gas, Water/Wastewater Management, Chemical Processing |
Key Benefits | Galvanic Corrosion Mitigation, Improved Cathodic Protection Efficiency, Prevention of Electrolytic Corrosion |
Related Technologies | Monolithic Isolation Joints (MIJs), Cathodic Protection (CP) Systems, Impressed Current Cathodic Protection (ICCP), Sacrificial Anode Cathodic Protection (SACP) |
Relevant Standards | ANSI B16.5 |
Reference Website | NACE International (The Corrosion Society) |
The selection of an appropriate flange isolation solution begins with a thorough assessment of the specific application. Factors such as the type of fluid being transported, operating temperature and pressure, and the surrounding environment all play a crucial role in determining the optimal FIK design and materials. Incorrect gasket selection, for instance, can have dire consequences, leading to isolation failure and subsequent mechanical issues. The goal is to create a leak-proof seal while simultaneously preventing the flow of electrical current between the metallic components of the pipeline.
Understanding Flange Isolation Kits
At its core, a flange isolation kit (FIK) is engineered to interrupt the metallic pathway between pipeline components, thereby halting the flow of electrical current and mitigating galvanic corrosion. Insulating flanges achieve this by incorporating non-conductive materials that separate the metal surfaces. These kits typically consist of an insulating gasket, insulating sleeves for bolts, and insulating washers. When properly installed, the FIK effectively breaks the electrical circuit, preventing the electrochemical reactions that drive corrosion.
Insulating flanges are essential components in cathodic protection (CP) systems, which are widely used to safeguard underground and above-ground pipelines from corrosion. By preventing electrolytic corrosion, these systems extend the lifespan of pipelines and reduce the risk of leaks and failures. An insulating flange may also be referred to simply as an isolation flange.
- Kannada Movies 20252026 Top Releases What To Watch Now
- Luke Combs Political Views Decoding The Stars Stance
The Anatomy of a Flange Isolation Kit
A standard FIK comprises several key components, each serving a specific purpose in achieving optimal isolation:
- Insulating Gasket: This is the primary sealing element that also provides electrical insulation between the flanges. Gaskets are available in various materials, including phenolic, G10, and other non-conductive polymers, each offering different levels of resistance to temperature, pressure, and chemical exposure.
- Insulating Sleeves: These sleeves are inserted into the bolt holes to prevent direct contact between the bolts and the flange metal, thereby eliminating another potential path for electrical current flow.
- Insulating Washers: Placed under the bolt head and nut, these washers further isolate the bolts from the flange, ensuring complete electrical discontinuity.
Single washer set flange isolation kits include these items for each threaded stud, ensuring comprehensive isolation at every connection point.
Gasket Types and Considerations
The selection of the appropriate gasket type is critical for the successful implementation of a FIK. Several types of gaskets are available, each designed for specific flange types and operating conditions.
- Type F Gasket (Ring Type): The gasket retainer extends out to the inner diameter (I.D.) of the flange.
- Full-Faced Gasket: These gaskets cover the entire flange face, providing maximum sealing surface area.
The threaded studs and sleeves are designed to center the gasket within the flange, ensuring proper alignment and even distribution of pressure. It's crucial that the bore of the flange isolating gasket matches the bore of the flange in which it is installed to prevent turbulence and potential erosion.
MIJ vs. FIK: A Comparative Analysis
While FIKs are a widely used solution for flange isolation, monolithic isolation joints (MIJs) offer an alternative approach. Both technologies aim to prevent corrosion, but they differ significantly in their design and application.
- Flange Isolation Kits (FIKs): These are installed between existing flanges and can be retrofitted into existing pipeline systems.
- Monolithic Isolation Joints (MIJs): These are pre-fabricated, single-piece units that are welded into the pipeline. They offer superior mechanical strength and long-term reliability but require more extensive installation procedures.
The decision to use an MIJ versus a FIK depends on various factors, including the specific application, budget, and desired level of protection. MIJs generally offer a higher level of corrosion protection and are often preferred in critical applications where long-term reliability is paramount. However, FIKs provide a more cost-effective and easily implemented solution for many pipeline systems.
Microbial Induced Corrosion (MIC) Considerations
Microbial induced corrosion (MIC) is a significant concern in pipelines, particularly those transporting water or wastewater. The presence of microorganisms can accelerate corrosion rates, leading to premature failures. When an FIK or MIJ is made to the pipe bore, this can dramatically reduce MIC issues by eliminating crevices where microorganisms can thrive.
Optimal FIK Performance: Key Essentials
Achieving optimal FIK performance requires careful attention to several key essentials:
- Proper Design and Fit: Ensure the FIK is designed to fit the specific flange type and operating conditions.
- Correct Material Selection: Choose gasket, sleeve, and washer materials that are compatible with the fluid being transported and the surrounding environment.
- Proper Installation: Follow the manufacturer's instructions carefully during installation to ensure proper sealing and electrical isolation.
- Regular Inspection and Maintenance: Periodically inspect the FIK for signs of wear or damage and replace components as needed.
A guide to optimal flange isolation kit (FIK) performance offers comprehensive insights and practical recommendations to help achieve superior results in operations.
Installation Best Practices
Proper installation is paramount to the success of any FIK. The following best practices should be followed to ensure optimal performance:
- Surface Preparation: Clean and inspect the flange surfaces to ensure they are free of debris and corrosion.
- Gasket Alignment: Carefully align the gasket with the flange faces, ensuring it is properly centered.
- Bolt Tightening: Tighten the bolts in a star pattern to ensure even distribution of pressure. Use a calibrated torque wrench to achieve the recommended torque values.
- Testing: After installation, test the electrical isolation of the FIK using a multimeter to verify that there is no continuity between the flanges.
Addressing Special Applications and Challenges
Certain applications present unique challenges for flange isolation. For example, pipelines operating at high temperatures or pressures may require specialized FIKs with enhanced sealing capabilities. Similarly, pipelines transporting corrosive fluids may necessitate the use of gaskets made from chemically resistant materials. A closer look at special/problem applications found across the globe reveals the diverse range of challenges faced by pipeline operators.
The Significance of "Full Length" Isolation Sleeves
Specifications for isolation sleeves often call for them to be "full length," but this term lacks a defined industry standard. It's essential to clarify the specific length requirements with the manufacturer to ensure the sleeves provide adequate isolation.
Flowcoating: An Alternative Coating Method
In addition to FIKs and MIJs, various coating methods are used to protect pipelines from corrosion. Flowcoating is a technique where a coating material is applied to a surface by flowing it over the part. Advantages of flowcoating over other coating methods include its suitability for large or oddly shaped parts that are difficult or impossible to dip coat. The advantages and limitations of the dipping process generally also apply to flowcoating.
Coal Tar Epoxy: A Durable Protective Coating
A coal tar epoxy is a black surface protection polymer used on surfaces subjected to extremely corrosive environments. It provides a robust barrier against moisture, chemicals, and abrasion.
ICCP Systems and Flange Isolation
Impressed current cathodic protection (ICCP) systems are frequently used to protect hundreds of miles of oil and gas pipelines. Electrical insulation is often provided between the flanges of connecting pipelines by using flange isolation kits to disrupt the electrical connectivity between adjacent pipes. This insulation improves the efficiency of ICCP systems by electrically isolating sections of the pipeline, allowing for more targeted and effective corrosion protection.
SACAP: Features and Benefits
Sacrificial anode cathodic protection (SACP) offers several advantages:
- No independent source of electric power required
- Limited affects on neighboring structures
- Anode connections are also protected
- No possibility of plant damage due to incorrect connections
Material Selection: Advantages and Disadvantages
Each material used in FIKs has its own set of advantages and disadvantages. Factors such as temperature resistance, chemical compatibility, and mechanical strength must be considered when selecting the appropriate materials. For instance, some materials are more forgiving to temperature application and surface preparation, while others may have low peel and shear resistance.
The Importance of Testing and Certification
Product testing and certification play a crucial role in ensuring the quality and reliability of FIKs. Products that have passed API 6FB fire testing, for example, demonstrate their ability to withstand extreme conditions. Electrical values are based on laboratory conditioned samples in laboratory conditions, providing a baseline for performance expectations.
Shell Global successful type acceptance test (TAT) certificate validates the performance and reliability of specific FIK designs.
The Velometer and Corrosion Assessment
A velometer is a device used to measure the speed of air in a given area. Often, the amount of air flow in the environment is directly proportional to the degree of corrosion experienced by a metallic structure and the drying rate of protective paints that are used to coat such structures. By monitoring air flow, engineers can gain insights into the potential for corrosion and adjust their protection strategies accordingly.
The Isoguard System
The Isoguard sealing/isolating gasket system is designed for general applications where electrical flange isolation and corrosion control are required on pipes containing water/wastewater, gas, natural gas, oil, and other hydrocarbon-based media up to 392F (200C). These gaskets resist oil, water, and salts, making them suitable for a wide range of environments. All gasket specifications are sized to meet ANSI standards.
Ramco Flange Isolation Gasket Kit (FIGK)
The Ramco flange isolation gasket kit (FIGK) is designed to be used on piping flanges & systems to provide cathodic protection, assist in the prevention of galvanic corrosion between the flanges, & isolate any current in the piping system from continuing down the line.
Transmuting Challenges into Opportunities
Advanced testing kits are invaluable tools for assessing the effectiveness of corrosion protection measures. By using these kits, pipeline operators can identify potential problems early on and take corrective action before they escalate into major failures. The alchemists guide to coatings: transmuting challenges into opportunities with advanced testing kits, is an apt metaphor for the proactive approach needed to combat corrosion.
Flange Isolation Kits: A Proven Track Record
Flange isolation gaskets and isolation kits are used throughout the world and in numerous cathodic protection industry applications. Flange isolation kits have a proven track record for being one of the most effective and reliable products for controlling and maintaining the integrity of piping and tank systems under demanding conditions.
Looking Ahead: The Future of Flange Isolation
The field of flange isolation is constantly evolving, with ongoing research and development focused on improving the performance, reliability, and cost-effectiveness of FIKs and MIJs. As new materials and technologies emerge, pipeline operators will have access to even more advanced tools for preventing corrosion and ensuring the long-term integrity of their assets. Guide to optimal flange isolation kit (FIK) performance; past, present & future.
ANSI B16.5 Specifications
Flange isolating gasket kits advance flange isolation gasket kits are manufactured according to ANSI B16.5 specifications up to 24". Above 24", please provide the specifications of your flange using our convenient worksheet. Technical assistance is available upon request.
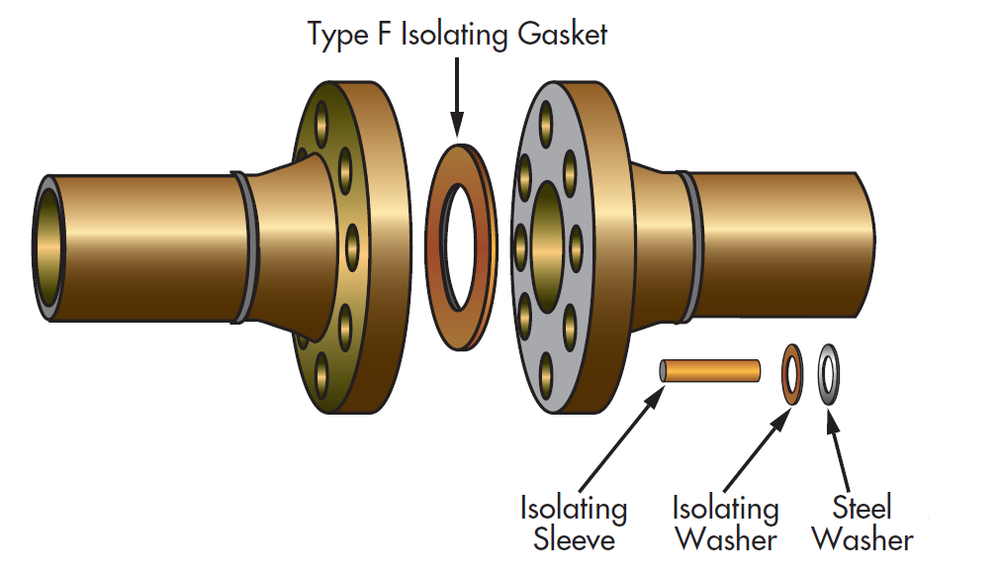


Detail Author:
- Name : Prof. Vickie Lindgren I
- Username : quitzon.bulah
- Email : qnader@yahoo.com
- Birthdate : 1990-02-20
- Address : 78567 Lindgren Underpass Suite 569 North Aureliobury, MD 54055
- Phone : 878-686-7595
- Company : Rosenbaum LLC
- Job : Gas Pumping Station Operator
- Bio : Eum inventore enim ut et omnis numquam. Eius sit accusantium qui eius reiciendis iure voluptatibus excepturi. Perferendis similique aspernatur enim est sequi.
Socials
facebook:
- url : https://facebook.com/janiyasauer
- username : janiyasauer
- bio : Laboriosam incidunt autem sit ad debitis. Excepturi beatae quod numquam hic.
- followers : 4905
- following : 2842
tiktok:
- url : https://tiktok.com/@jsauer
- username : jsauer
- bio : Iste in sed et rem. Consequatur quis voluptatibus qui iste veritatis sit.
- followers : 2355
- following : 2556
linkedin:
- url : https://linkedin.com/in/janiya.sauer
- username : janiya.sauer
- bio : Nihil id officiis quam nihil vel animi.
- followers : 2131
- following : 1506
instagram:
- url : https://instagram.com/janiyasauer
- username : janiyasauer
- bio : Dolorum esse quis rerum dolor. Sint et ea maxime deleniti qui. Amet ut et hic ipsa ducimus dolores.
- followers : 2831
- following : 2543